Understanding UV Curing
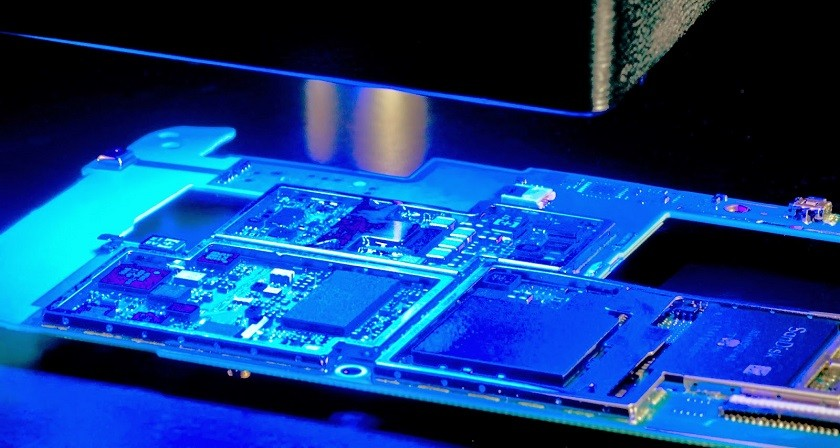
UV curing is the crosslinking of polymers through a photochemical reaction initiated by ultraviolet light. The process was invented in the 1960s to speed up the drying of inks on printed fabrics, among other applications. Currently, manufacturers of UV curing systems, such as Omnicure, produce systems suitable for all applications. UV formulations, monomers, and oligomers are mixed with photo-initiators then exposed to ultraviolet energy. The formulations, such as inks, instantly harden when exposed to ultraviolet light, ready for the next process.
Applications of UV curing
UV curing is applied in various industries. These include;
Printing
Modern-day printing largely depends on UV curing. In screen printing, UV curing is used to polymerize images on printed items such as fabrics. UV curing is one of the oldest and significant technologies adapted in 3D printing. The UV laser continuously shifts position while curing regions of polymers. The continued shifting in position and curing results in a solidified 3D structure. The rapid photochemical reactions generate high-resolution finished products.
Metal coating
Metal coating is an important industrial process. The process is applied in the manufacture of insulated cables, among other items. The coating materials are applied on the metal surface according to the specifications provided. Once the coat is applied, the metal is then exposed to ultraviolet light. The coating material then solidifies through photoelectric reactions induced by the ultraviolet light.
There are many other applications of UV curing; these include applications in the field of medical device manufacturing and packaging services.
Advantages of UV curing
UV curing has several advantages, hence the reason for its increased popularity in different industries. These advantages include;
Time-efficient
Curing of substances with ultraviolet light takes a shorter time to be complete. The photoelectric reactions in UV curing are rapid, thus, speeding up the drying step in printed or coated items. Reducing the time items spend when wet contributes to greater consistency and high-quality finishes. Additionally, more space for storage is created when items spend minimal time in the curing process.
Applicable to many industries
UV curing is applicable in almost all industries that require curing as part of the processing procedures. Ultraviolet reacts differently with various materials; this allows for production of items that are not achievable by other curing means. With UV curing, specific levels of strength, hardness, and durability for items can be achieved.
Disadvantages of UV curing
Despite its importance, UV curing comes with various disadvantages. These include;
High cost of UV curing systems
UV curing systems are relatively expensive, depending on the purpose they are sought for. The technology involved in the production is costly; this results in higher prices when acquiring the system. Some UV curing systems use a lot of energy to deliver quality results. The energy consumed by the systems leads to huge power bills and other maintenance costs.
Risk of burns to operators
UV curing systems produces a lot of heat when in use. An operator can get burned if they accidentally touch some parts of the systems. Additionally, some UV systems emit very bright visible light, which can be harmful to an operator’s eyes.
UV curing systems should be purchased from accredited manufacturers such as Omnicure for safety and efficiency.